To see this article please enter to AWS, this article belongs to AWS :
Resistance welding (RW) is a thermo-electric welding process in which the weld is made by a combination of pressure and current. The process involves the joining of metals by applying controlled pressure and passing current through the metal area to be joined. There are several different forms of RW (e.g., spot, seam, projection, single-sided, bonding, cross wire, micro, flash, and upset welding) that differ primarily by the types and shapes of weld electrodes used to apply the pressure and conduct the current.
Photo: Resistance welding is a thermo-electric process in which heat is generated at the interface of the parts to be joined by passing an electrical current through the parts. There are several different processes of resistance welding, including spot welding.
The electrodes, typically manufactured from copper-based alloys due to their superior conductive properties, are cooled by water flowing through cavities inside the electrode and the other conductive tooling of the RW machine.
There are several key advantages of the RW process, including the following:
-Very short process times;
-No consumables, such as brazing materials, shielding gas, solder, or welding rods/wires;
-Operator safety because of low voltage and fume emission;
-Cleanliness and environmentally friendliness; and
-Formation of a reliable electro-mechanical joint.
Safety Hazards
RW is not an open-arc process, and the weld is made inside or between the workpieces. As a result, several unique hazards must be considered during RW:
-Flying sparks can cause fire and explosion.
-Flying sparks and spatter can burn or injure eyes and skin.
-Electric shock can occur from live electrical parts.
-Hot metal and parts can cause burns.
-Moving electrode parts, such as tongs, tips, and linkages, can injure fingers and hands.
-Spot welding parts coated with cleaners, paints, or platings can create fumes.
How to Avoid the Hazards
The following lists several ways to stay safe during RW:
-Wear the appropriate personal protective equipment, including safety goggles or a face shield/safety glass; long-sleeved shirts made from nonmelting material; and dry, insulated gloves.
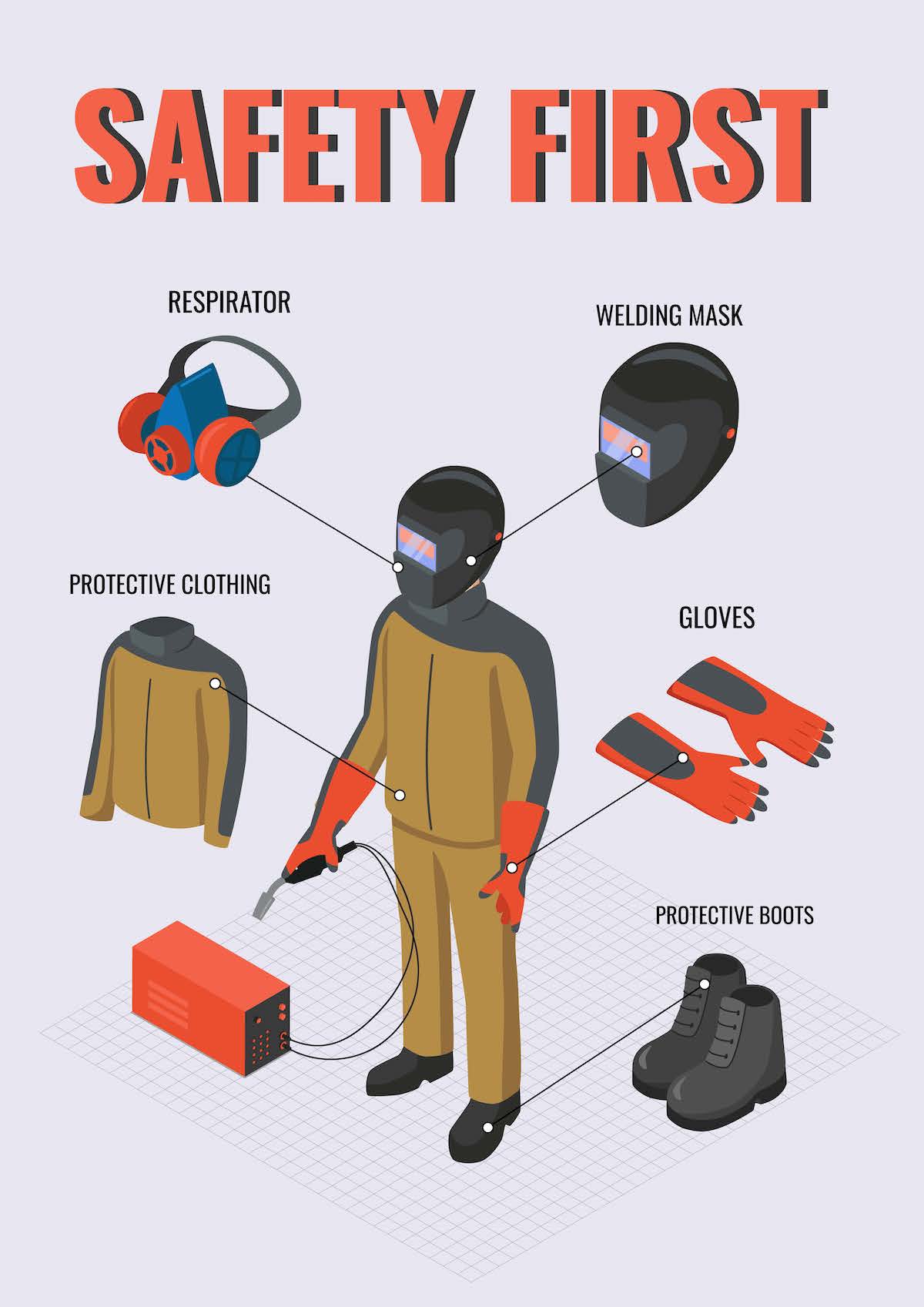
-Do not weld near flammables (move flammables away from the welding area). Also, keep a fire extinguisher nearby and know how to use it.
-Do not breathe the fumes. Use adequate ventilation and read safety data sheets for metals, coatings, and cleaners.
-Do not put your hands between tips. Keep away from linkages and pinch points. Keep all guards and panels in place.
-Do not touch hot workpieces, tips, or tongs with your bare hands. Allow tongs and tips to cool before touching. Wear proper insulating gloves when handling hot work or parts.
-Install and ground the unit according to electrical codes. Grounding should be provided to the secondary of all welding transformers for multispot, projection, and seam welding machines.
-Disconnect the input power before servicing. Ensure all equipment, with an appropriate safety disconnecting switch or circuit breaker, has been installed by qualified electricians.
-A thermal protection switch should be provided for ignition tubes used in RW equipment.
-Keep guards in place to mitigate activation of all automatic or air and hydraulic clamps, including foot pedals/switches.
-Use complete enclosures to insulate and protect stored energy or capacitor discharge types of RW equipment and control panels involving high voltage, including door interlocks that interrupt power and discharge capacitors.
-Use electronic eye, two-hand controls, or protection similar to punch press operation as guarding for all press welding machine operations when there is a possibility of the operator’s fingers being under the point of operation.
Adapted from American Welding Society (AWS) Safety and Health Fact Sheet No. 21, Resistance Welding. All of the AWS Safety and Health Fact Sheets are available through the AWS website at aws.org. Click on Standards on the home page and then on Safety & Health. AWS disclaims liability for any injury to persons or property, or other damages of any nature whatsoever, whether special, indirect, consequential or compensatory, directly or indirectly resulting from the publication, use of, or reliance on this information. AWS also makes no guaranty or warranty as to the accuracy or completeness of any information published herein.https://www.aws.org/magazines-and-media/magazine-and-journal/welding-digest/welding-digest-staying-safe-during-resistance-welding/